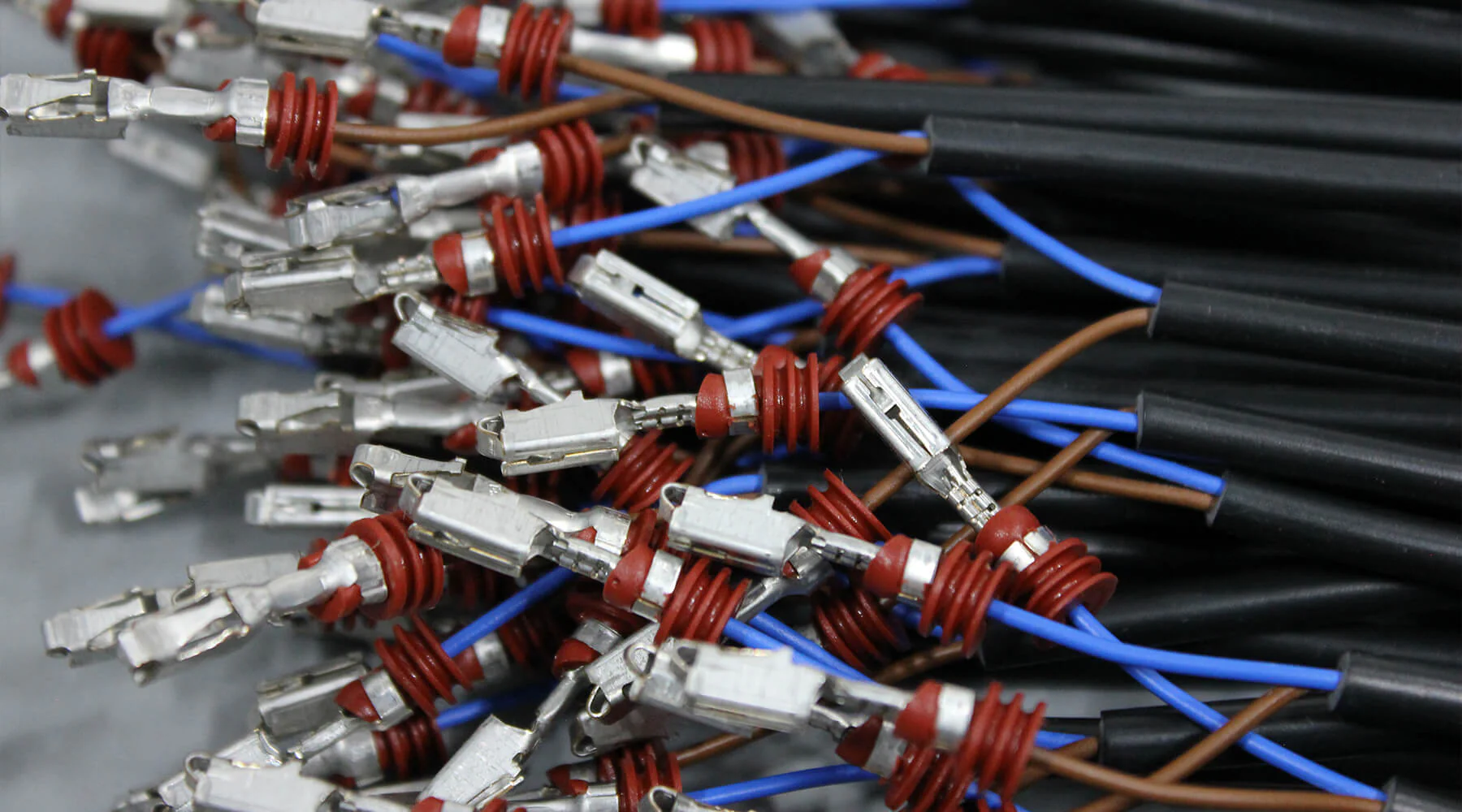
How Can I Validate the Crimp Quality?
Using the right crimping tools and connectors is good. However, ensuring that a crimp joint is securely connected and functioning properly is an extremely important part of the crimping process. Usually, a visual inspection isn’t enough to verify the quality of a crimp.
Importance of Validating Crimp Quality
You’re probably wondering why validating the quality of a crimp is that vital. The ultimate goal of every crimp joint is to have mechanical strength and low electrical resistance on crimp joint.
Also, you must ensure your crimp joint are gas-tight. It prevents moisture and oxygen from forming corrosion on the crimp joint. Another aspect is that validating quality helps you ensure the crimp joints aren’t over-tightened: over-tightening could damage the wires (ultimately leading to loss of electrical continuity) or increase electrical resistance. Above all, a high-quality crimp can last for a long.
Ways of Validating the Quality of a Crimp Joint
1. Pull force test
Pull force test is one of the basic ways to verify the quality of crimp joints. Generally, you could say this approach tests the mechanical strength of a crimp joint.
It entails using a motorized pull tester that pulls the wire from the terminal at a steady rate/ constant speed to measure the force required before a wire breaks from the crimped terminal. The result is compared to industry standards (a minimum acceptance value for the pull force according to the wire diameter and AWG conductor size). For instance, an 18 AWG wire should withstand a minimum of 20lbs of pull force on the conductor crimp.
The only downside of the pull force test is that it’s destructive: it puts strain or completely breaks a crimp joint. However, it can effectively assess the integrity of the crimping tool used to make the crimp. As a result, you can calibrate the crimping according to the results.
2. Electrical resistance test
The electrical test is another practical way to validate the quality of the crimp. It entails connecting the milli-ohm meter to the crimped terminal and on the other end of the wire. However, you should consider cutting back the wire and stripping it close to the crimp for the best results.
However, this test is also considered destructive but is helpful in verifying crimp joint quality during setup and spot checks.
3. Cross–section analysis
Cross-section analysis involves cutting the crimp into half to access and inspect the cross-section area of the crimp. The area is then polished and etched before it’s put under a microscope to check the condition of the wire strand compression.
As seen on a magnified image, a deformed wire, a symmetrical wing, and visible blades/anvil signifies a properly crimped cross-section. If the crimp flags are touching the terminal floor or there is uneven wire distribution, that’s a sign of poor crimping.
4. Crimp height measurement
Another way to validate the crimp quality is by measuring crimp height. It helps determine whether the crimp compression meets certain specifications. This process requires using a Crimp Height Micrometer, especially a digital one. It has a unique anvil and spindle configuration that enhance precision in measurement in crimped electrical contacts.
Crimp height measurement will help you identify any crimping inconsistency and wear on your crimping tool. The only downside of this method is that it’s time-consuming.
5. Crimp force monitoring
Lastly, you could opt to use a crimp force monitoring system often used with bench-top crimp presses and automated crimping machines.
As the name suggests, it measures the crimp force of each termination in real-time during the crimp cycle. It then uses a control unit to analyze data to determine whether a crimp is good or defective.
A crimping force monitoring system can easily detect issues with wrong wire gauge, poor insulation and the presence of wire strands. However, false readings is a concern with this particular method of validating crimp quality.
Bottom line
Quality assurance is vital when creating wire crimps for your DIY or professional projects. For harness manufacturers, validating crimp quality is a non-negotiable function that helps them meet customers’ specifications. Overall, quality crimps help minimizes issues such as thermal stress on electrical connections. To verify the quality of the crimp joints, use any of the above methods. However, you can complement one method with another for more effective results.
References